How California museum is protecting space shuttle Endeavour against earthquakes
'Suffice it to say that the building and Endeavour will be standing when L.A. is a pile of rubble.'
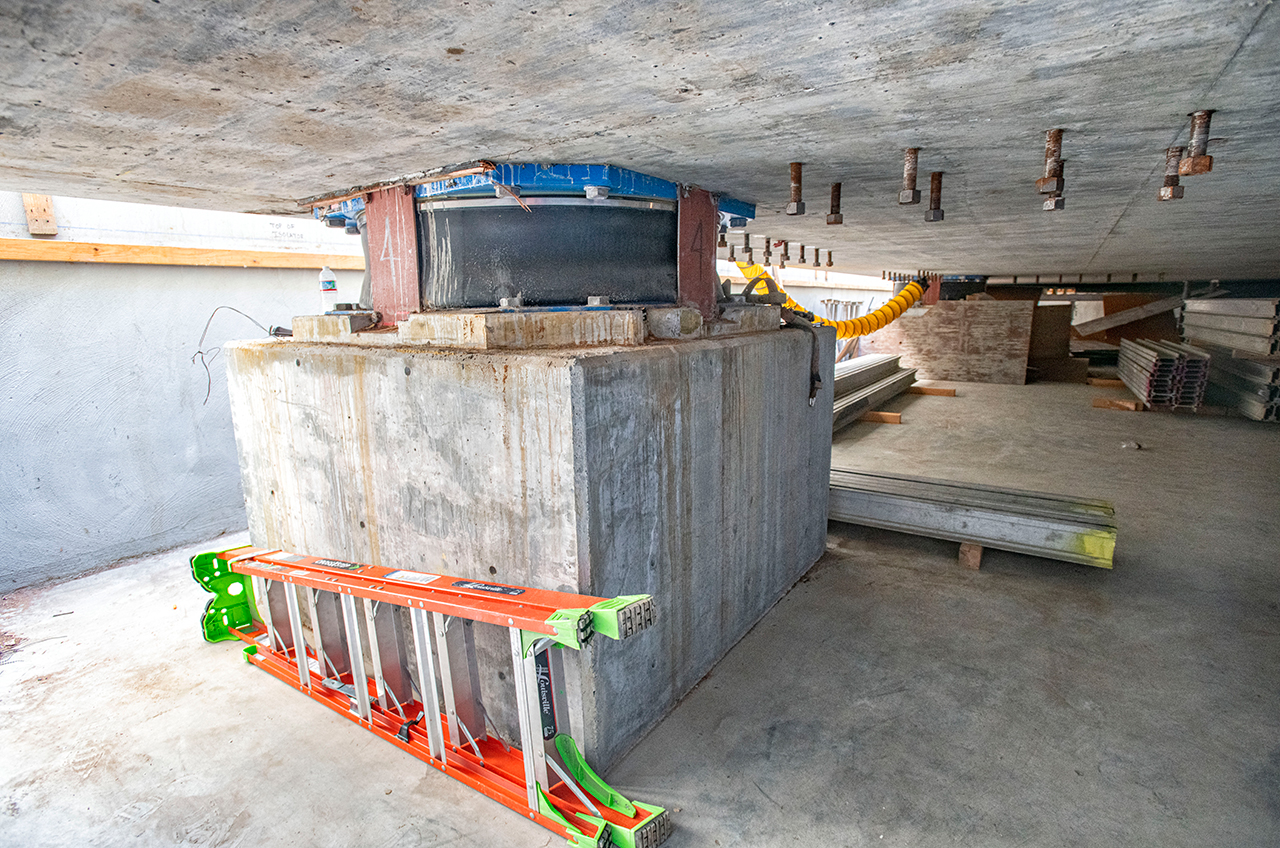
Even before it opened more than a decade ago, the exhibit of NASA's retired space shuttle Endeavour in Los Angeles has elicited one question perhaps more than any other: Can it survive an earthquake?
And to think, that was while the winged orbiter was displayed near the ground in its horizontal, landing configuration.
Now, as the California Science Center takes the first steps to stack the vehicle with a pair of twin solid rocket boosters and an external fuel tank for a vertical, launchpad-like permanent exhibit inside the new Samuel Oschin Air and Space Center, the question has only increased in magnitude.
"Suffice it to say that the building and Endeavour will be standing when L.A. is a pile of rubble," Dennis Jenkins, director of the science center's project to display Endeavour and a former NASA space shuttle engineer, said in an interview with collectSPACE.com.
A lot of research and technology stands behind Jenkins' answer, providing the confidence for he and his team to go forward with stacking the towering display.
Related: Where are NASA's space shuttles now?
7,383
When Endeavour was rolled into its pavilion at the end of a three-day road trip in October 2012, it was mounted atop four friction-pendulum seismic isolators. In the case of a powerful earthquake, the shuttle would only glide gently back and forth, having been separated from the ground.
Since that day, Caltech's Southern California Earthquake Data Center has recorded 7,383 times the the ground shook strongly enough that people in the area might feel it. Five of those events were violent enough to cause minor damage. And one, a 7.1 magnitude earthquake in 2019, was felt by as many as 30 million people spanning the length of the state.
"The only one that I remember was the largest one," said Jenkins. "We went through and looked at the surveillance cameras, and there was no movement [of Endeavour] — or at least, none that we could perceive."
The same type of isolators are part of the way that Endeavour will be kept safe in the vertical configuration, though the preparations and complexities involved are greater.
Stress test
If you've been to the California Science Center to see Endeavour since it opened on display, you may have met Bill Novak. He is one of the docents helping to answer guests' questions as they tour around the exhibit.
Novak also happens to have been the lead of the shuttle loads group at Boeing (and Rockwell before that).
"He and several of his former coworkers provided a great deal of input on how the vehicle reacts to loads," said Jenkins, adding that the structural engineers for the Oschin Air and Space building took the lead in the earthquake studies, but had no experience with spaceflight hardware. "Once the two groups developed a common language — structural engineering uses different terminology than aerospace engineering — it went pretty smoothly."
What the two groups of engineers ultimately found surprised them both. Where initially Jenkins' team thought there was an advantage to using replica hardware to incorporate or hide earthquake protection systems, the studies found what was needed was the real thing — parts that, like Endeavour itself, were built for flight.
"Perhaps the most critical outcome of the seismic studies was that, although vastly different from flight loads, the seismic loads were completely enveloped by the loads the space shuttle stack was designed to endure during ascent. This meant that we did not need to make any modifications to the stack hardware, but it also meant that we needed to use flight hardware in all of the critical applications, since that is what we modeled for the seismic studies," Jenkins said.
In the end, the only critical components that the science center could not source from the leftovers of the space shuttle program were the two rings that connected the solid rocket booster to the aft external tank. Instead, they had a local aerospace machine shop build a set to the original specs as the flight hardware so they were essentially interchangeable.
By using all flight hardware — including the last existing external tank built for flight and twin boosters built up from previously flown segments — the space shuttle's ultimate design loads were about 5% greater than the "maximum credible event."
"So they are somewhat higher than the worst-case flight loads, but still within the capability of the vehicle to survive without permanent damage," said Jenkins.
Related: Facts about NASA's space shuttle, the 1st reusable spacecraft
Skirting the issue
On Thursday (July 20), if all went to plan, the first large components of the shuttle stack were hoisted by crane and lowered into their place inside the still-under-construction Oschin Air and Space Center. The two solid rocket booster aft skirts are the first major parts to be moved, but they are preceded by other hardware that will protect Endeavour's vertical display.
The aft skirts are being seated atop an 8-foot-thick (2.4 meters), 1,800-ton slab of reinforced concrete that is supported by six triple-pendulum isolators manufactured by Earthquake Protection Systems, Inc. (EPS), the same company that furnished the isolators for Endeavour's horizontal display.
Get the Space.com Newsletter
Breaking space news, the latest updates on rocket launches, skywatching events and more!
"There is a 3-foot (0.9 m) moat around the floating concrete slab so it can move three feet in any direction," said Jenkins. "We don't dampen vertical motion, so whatever vertical motion the earthquake gives us is what we get, but horizontal motion we can move three feet in any direction."
The stack will then be secured to the slab using the eight solid rocket booster "hold-down" posts on the aft skirts, the same ones used to secure the shuttle to its mobile launch platform when it was standing poised for launch.
"Our hold-down hardware is a bit different but conceptually identical — a hold-down stud with spherical bearings and a nut on the bottom and a spherical bearing and spherical nut on top. The two largest differences is that our hold-down studs are 9 feet long (2.7 m), versus 31 inches (79 centimeters) for the flight studs, and our spherical nut is not equipped with pyros to blow it at T-0," Jenkins said.
Follow collectSPACE.com on Facebook and on Twitter at @collectSPACE. Copyright 2023 collectSPACE.com. All rights reserved.
Join our Space Forums to keep talking space on the latest missions, night sky and more! And if you have a news tip, correction or comment, let us know at: community@space.com.
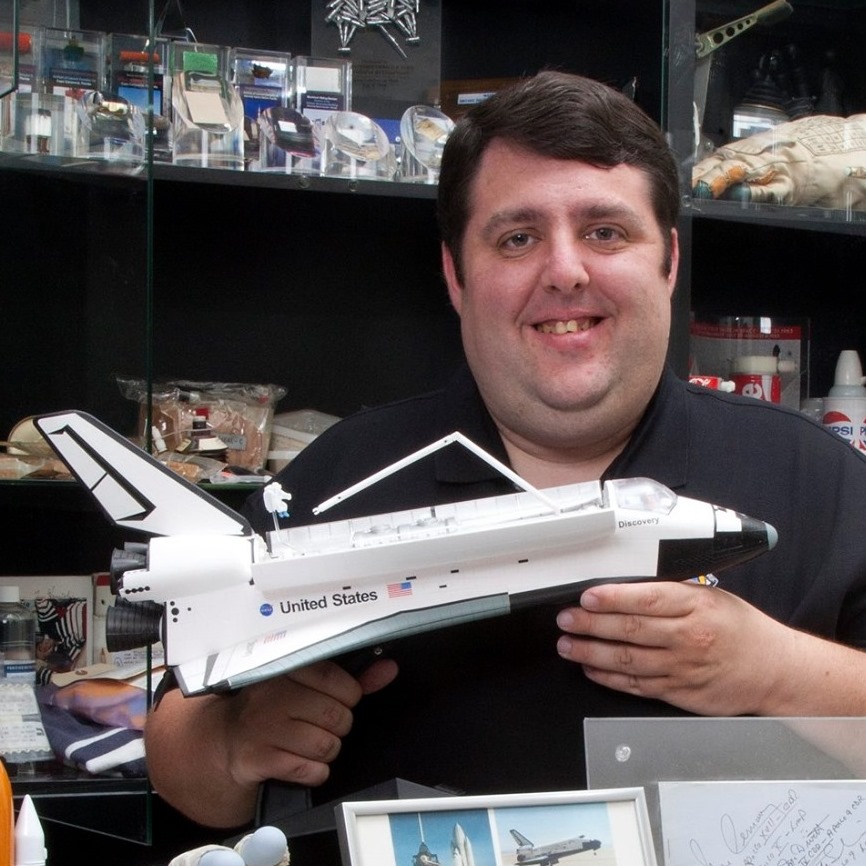
Robert Pearlman is a space historian, journalist and the founder and editor of collectSPACE.com, a daily news publication and community devoted to space history with a particular focus on how and where space exploration intersects with pop culture. Pearlman is also a contributing writer for Space.com and co-author of "Space Stations: The Art, Science, and Reality of Working in Space” published by Smithsonian Books in 2018.In 2009, he was inducted into the U.S. Space Camp Hall of Fame in Huntsville, Alabama. In 2021, he was honored by the American Astronautical Society with the Ordway Award for Sustained Excellence in Spaceflight History. In 2023, the National Space Club Florida Committee recognized Pearlman with the Kolcum News and Communications Award for excellence in telling the space story along the Space Coast and throughout the world.